EPP
The particle foam EPP (Expanded Polypropylene) helps to save weight, energy and time.
The full design freedom gives designers and engineers the chance to unleash their creativity and offers unparalleled opportunities for creating designer products, designing technical shaped components and redesigning metal components.
Shaped components made from EPP are sustainably produced by the particle foam engineers at HSV, and assembled according to specifications. EPP is sustainable and can be completely recycled
EPP | Exceptional set of material properties
In addition to full freedom of design, EPP offers an exceptional set of material properties. Protection, insulation and assembly are combined in this particle foam. EPP is lightweight, very resilient, has thermal insulating properties, low compressibility and is easy to clean. Thanks to its shock-absorbent capacity, EPP easily returns to its original shape. As a result, the material is used widely in all markets. EPP properties at a glance:
- Freedom of design & engineering
- Lightweight, leading to a range of savings
- Easy to clean and resistant to chemicals
- Shock-absorbent and multi-resistant properties
- Thermal insulating λ (0.035 – 0.041) (W / mK) and acoustic damping
Download EPP data sheet:
EPP | High-quality protection
EPP offers high-quality protection during transport of valuable goods, medical products and donor organs. As an added bonus, it helps the transport sector save fuel and energy. Used in such applications as body protectors, rescue equipment, head protectors, bumpers and side crash pads, EPP contributes to your safety, thanks to its shock-absorbent properties.
EPP | Thermal insulation, acoustic damping and shock absorption
A thermo box made from EPP keeps food at the right temperature, keeping it fresh for days. Supermarkets, caterers, restaurants and web shops can easily respond to growing consumer demand in convenient ways.
When used in insulation materials, it keeps our homes comfortably warm in winter and cool in summer.
In HVAC products, such as heat recovery units, central heating boilers and equipment housing, EPP not only provides thermal insulation, but also reduces noise and improves shock absorption
EPP | Construction material
EPP is strong and can be used in construction materials. It has an extremely high strength-weight ratio and can take significant loads over and over. Thanks to its high energy absorption and resilient properties, it retains its shape after static or dynamic load.
EPP | Resistant to chemicals
EPP absorbs very little moisture, is easy to clean, and resistant to oils, fats and many chemicals. In addition, EPP is impervious to microbial growth and resistant to chemicals. That is why EPP is also widely used in the medical industry, for example in transporting fragile medical equipment and donor organs, even into the operating room.
EPP shaped components | Density, colour and finish
EPP shaped components can be produced in various densities. EPP comes in various colours, and you can have HSV add a wide range of finishes and surface treatments to your product
EPP | Closures and connections
Closures and connections can also be added, including all sorts of click and screw fastenings, plugs, brackets and hinges. Options also include efficient combination and assembly of niches, channels, added components, motors and cables. This helps you achieve savings in your logistical process. You can find more information about this on the assembly page.
EPP and the environment
EPP is a monomaterial. That means that EPP is made from one single type of material: polypropylene. As a result, EPP is easy to recycle. During the production process, the particle foam engineers at HSV use green steam (100% water) and green energy, generated from renewable energy and solar power.
EPP is a lightweight material, making it extremely suitable for use in the transport sector. The lower weight also reduces the carbon footprint and achieves savings on fuel and energy in the logistical process. And that is better for the environment.
Production process for EPP shaped components
Products, housings and semi-manufactured products made from EPP are sometimes referred to as EPP shaped components. To produce EPP shaped components, the particle foam engineers at HSV use autoclave technology. This involves placing a matrix or mould in the shaped component machine.
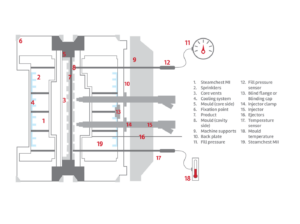
Details of a mould
The EPP pellets (also known as beads or particles) are injected into the mould under high pressure. Then steam is used to heat the material to approximately 140 tot 165°C, depending on the type of raw material used.
The EPP pellets expand and melt together, taking on the shape of the mould cavity. This shaped component process is better known as particle foam engineering.
![]() EPP shaped component process |
![]() EPP pellets expand |
After release from the shaped component machine, the EPP shaped components are dried in drying chambers, taking on their final stability.
Request a Feasibility Study
Are you curious about the feasibility of your product design in EPP?
Whether you have an idea, sketch or prototype, the Feasibility Study conducted by the particle foam engineers at HSV analyses and assesses how feasible it will be to produce or redesign your envisioned product. Based on the Feasibility Study:
- You will receive advice without any obligations
- You will gain insight into the options for your finished and/or semi-manufactured product, and find out how long production will take
- You will receive an initial estimate of the costs
Click the button below to request a Feasibility Study now. Your request will be kept confidential.