Assembly at HSV – Innovation in fixation
Automated fixation of inserts in EPP parts, to connect other materials – LiteWWeight® zEPP
This article was a joint effort, with special thanks to Christian Busch, Business Development Manager for MM-Welding technology [Bossard] and Ivo Ariens, Technical Director, Antwan Veldhuizen, Product Engineer and Torsten Kley, Key Account Manager with HSV Packaging & Insulation NV, also known as the particle foam engineers at HSV.
Christian Busch launches into the topic: ‘As Business Development Manager for MM-Welding technology at Bossard, I advise organisations on such topics as fixation technologies. HSV Packaging & Insulation NV is the first manufacturing company to use an innovative fixation technology for a standard EPP application. This involves LiteWWeight® zEPP, which is part of a broader technology platform known as MultiMaterial-Welding [MM-Welding®].’
Christian continues: ‘Torsten Kley facilitated contact with Ivo and Antwan, from the particle foam engineers at HSV, when they were looking for a solution to optimise fixation of inserts, to connect EPP parts with other materials.’ Torsten adds, ‘Bossard has the equipment and fixation technology available to achieve high-quality fastenings that deliver stable performance. The quality of the connection is already measured during the fixation process, assisted by artificial intelligence and big data. That makes this solution very interesting to HSV and its customers, which inspired me to reach out,’ Torsten explains. ‘As you can imagine, this offers all sorts of advantages.’ More on that later…
![]() |
![]() |
![]() |
Example: Fastening insert in EPP component using LiteWWeight® zEPP and MM-Welding® technology
‘HSV Packaging & Insulation NV is the first manufacturing company to use LiteWWeight® zEPP, the innovative fixation technology, for a standard EPP application’
Christian Busch
Business Development Manager | MM-Welding technology | Bossard
High-quality fixation for EPP parts
Ivo Ariens offers further details: ‘For one of our customers, we were looking for a solution that would specifically contribute to faster, high-quality fixation of inserts, which are used to connect EPP parts with other materials. In addition, we wanted to accelerate and streamline the assembly process. Torsten came across this innovation and took the initiative to arrange an initial meeting to explore options with Christian and introduce this novel solution. After performing various tests and experiments, our R&D department was soon convinced. The combination of MM-Welding® technology and LiteWWeight® zEPP gives HSV options for even more efficient fixation of inserts in EPP shaped components.’
Watch the video and discover more
Advantages for our customers
Ivo explains: ‘This solution also yields significant savings in the overall assembly process. This translates into a number of interesting advantages for our customers, including reduced costs and improvements in the finished product. The technology also offers more freedom of design for engineers and product designers.’
✓ Reduced costs
✓ Improved products
✓ More design freedom
MM-Welding® technology and LiteWWeight® zEPP give HSV options for even more efficient fixation of inserts, which are used to connect EPP shaped components with other materials. This solution also yields significant savings in the overall assembly process
Product Engineer Antwan Veldhuizen adds, ‘The fastenings achieved using this fixation technology are significantly stronger, compared to various other fixation methods. It also contributes to tolerance compensation without precise alignment in advance.
Advantages compared to traditional fixation methods:
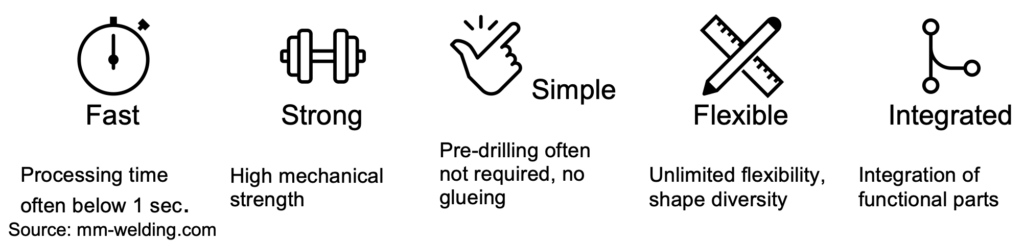
Deploying a statistical check based on MM-Welding® SmartSolutions, measurements are performed during the fixation process, guaranteeing the quality of every fastening. And the process is clean, without any need to pre-treat the surfaces or incorporate extra materials. As a result, there is hardly any waste, which is better for the environment.’
SmartSolutions
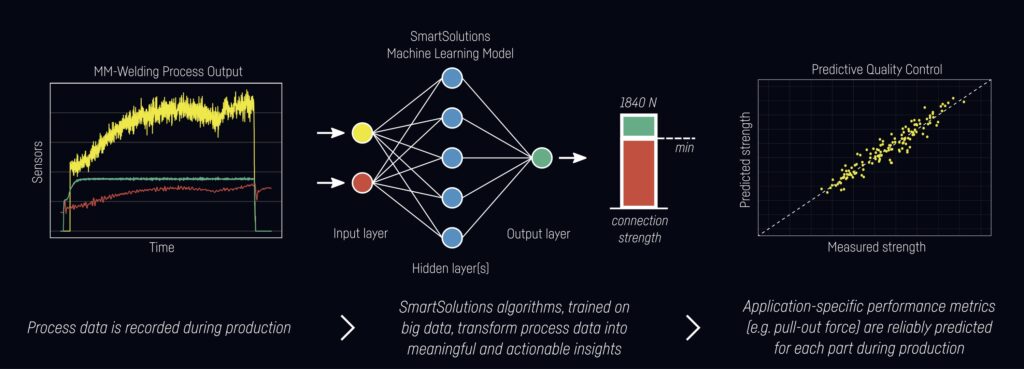
‘The quality measurements are performed using SmartSolutions.’ Christian explains: ‘SmartSolutions offers the option for quality control of 100% of the parts that are produced, providing valuable and actionable insights. The software is based on machine learning applied to real-time production data, unlocking the potential of artificial intelligence and big data. This method eliminates the need for destructive testing.’
‘The fastenings achieved using this fixation technology are significantly stronger. The quality of every fastening is guaranteed during the fixation process’
The machine is now being used by the assembly department at our production location in Ede. Following a training session for the assembly team, the first EPP parts have been attached with inserts using MM-Welding® technology. |
|
‘We are already experiencing the benefits. The fastenings deliver stable quality and strong fixation, the waste flow has been reduced, and the process is more efficiently structured,’ Ivo reports enthusiastically.
Efficient assembly
Do you have questions about efficient assembly of particle foam components after reading this article? Or would you like to explore the feasibility of your product concept?
The particle foam engineers are at your disposal and would be happy to brainstorm with you about the most ideal solution for your product or shaped component. Click the button below to request a free feasibility study. Your request will be kept confidential.
The feasibility study will also look at lead time and cost-efficient solutions in the production, assembly and logistics processes.
More about MM-Welding® technology
MM-Welding® is an innovative fixation technology that uses ultrasonic energy to create a frictional positive connection in porous materials. Based on the sophisticated MM-W process technology, specific solutions have been developed to fasten EPP shaped components with other materials. A ball-head pin or double pin fastener is used to connect components, achieving fast and strong fixation.
Downloads
Or watch the video and get an impression:
This technology is applied in various industries (including medical applications and furniture-making) and can be used to connect particle foam components, composite structures, sandwich panels, injection-moulded and compressed parts.